Everyone related to the construction process has an incentive to get the project done faster and at a lower cost – from the project owners who want to see results for their investment to the contractors and designers who want to do their job well and move on to the next project. Lean Construction is based on the holistic pursuit of continuous improvements aimed at minimizing costs and maximizing value on a construction project: planning, design, construction, activation, operations, maintenance, salvaging, and recycling.
To help contractors develop the knowledge needed to build Lean, the Associated General Contractors of America developed the Lean Construction Education Program (LCEP). Construction professionals at all experience levels will learn the building blocks necessary to transform their projects and companies into a Lean Operating System.
The highly interactive program provides 36-hours of instruction and training to provide construction industry professionals at all levels with the knowledge and skills to take advantage of the benefits of Lean Construction.
Students participating in AGC’s five-unit Lean Construction Education program will be eligible to take an exam to earn their CM-Lean.
The AGC Certificate of Management-Lean Construction (CM-Lean) is an assessment-based certificate credential that denotes knowledge and understanding of concepts related to lean adoption, practice, and process transformation outlined in AGC’s Lean Construction Education Program. Successful candidates will carry the CM-Lean designation.
Course Overview
Upcoming Courses
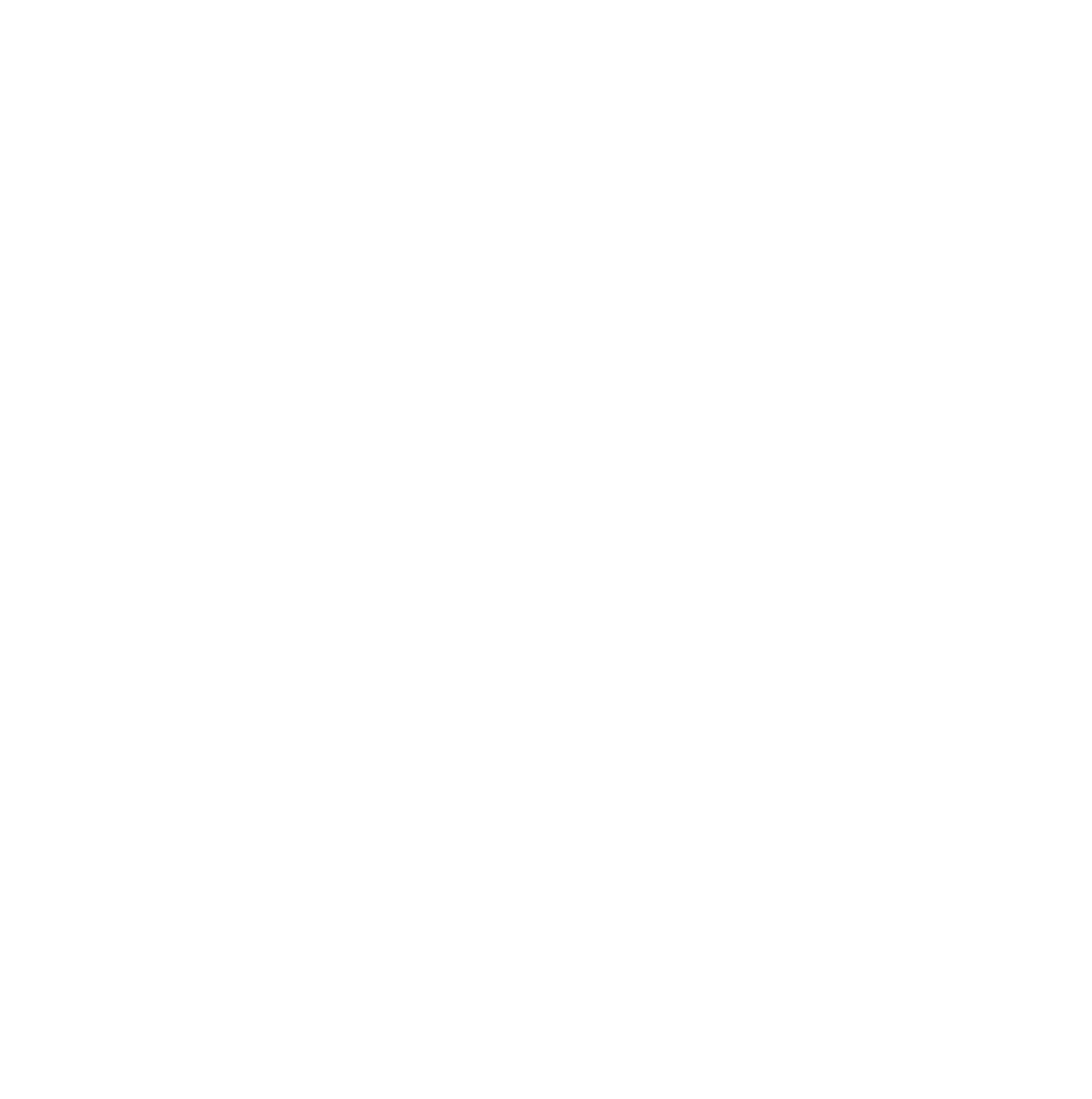